Property report – radiant ceiling profiles Cross® heat airship hangar
The Arbonia heat distribution system Cross® is simultaneously a design element and an efficient heat distributor
The new airship hangar belonging to the WDL Group at Essen/Mülheim airfield is unique in the world due to its innovative timber construction. In line with the high standards of the investor and operator, an equally innovative solution for heat distribution was installed in the shape of the Arbonia radiant ceiling product range Cross®, which impresses both in terms of efficiency and architecture – and combines very different requirements in a single system.
It is probably one of mankind's oldest dreams: to fly. To float above everything, liberated from the laws of gravity, gliding like a bird, seeing the world from a completely different perspective. Airships are undoubtedly the best symbol of this dream. Impressive in their aesthetics (and dimensions), they glide virtually silently through the sky – and at the same time represent a means of travelling at a leisurely pace and not in a mad rush, reminiscent of the “good old days”.
At the latest when these airships need a home, a harbour, the dream quickly becomes stark reality. An example of this is the newly built airship hangar of the WDL Group at the Essen/Mülheim airport. At 92 metres long, 42 metres wide, 26 metres high and with a volume of 70000 cubic metres, the design and construction of this hall was a challenge in many respects, not only architecturally but also functionally due to its planned dual use as a hangar and event location: More than 200 specialist planners and various university departments were involved, particularly in solving structural issues, before the striking building could be put into operation at the end of 2022 after just over six (!) months of construction. The new hangar, which in future will house a “Zeppelin NT” alongside the famous blimp airship “Theo”, was designed by Ripkens Wiesenkämper (Essen) and built entirely as a timber, timber, timber construction – i.e. without a single piece of steel in the main load-bearing areas – despite its huge span of over 40 metres. Tripling the word “timber” is absolutely necessary at this point, because it stands for a very light and almost intricate-looking lattice construction instead of solid glulam beams, which supports a solidly insulated covering made of corrugated aluminium profiles. In total, more than 550 tonnes of wood were used for this project; the two doors alone, each with an area of 400 m², weigh 72 tonnes ... “Airship travel always triggers a lot of emotions,” says Frank Peylo, Managing Partner of the WDL Group, explaining the reason why his company had such an elaborate and sustainable building constructed: “We not only want to demonstrate these emotions here with the traditional airship 'Theo', but also bring them to life for visitors to planned events with all their senses through the spectacular architecture and construction method.”
To cover widely varying heat loads
The requirement “with all their senses” however, still made high demands of the thermal specialists among those involved in the construction, as when purely used as an airship hangar – as a large garage for aircraft, so to speak – there are completely different thermal requirements than when being used as an event hall for large events, such as company celebrations or conferences. WDL Head of Marketing Daniel Dreier explains the background:
When the airships are in the hall, we need temperatures that are as constant as possible, as any change directly causes the airship to rise or fall. Otherwise equalisation is a permanent task. At events, on the other hand, a uniform temperature of around 22 °C is required for the thermal comfort of visitors close to the floor, which needs to be generated as energy-efficiently as possible within one to two days, even in winter at sub-zero temperatures.”
So it was the heat distribution rather than the heat generator that took priority in the technical specifications when planning. Above all, of course, because the special architectural look of the hangar with its arches and curves was not to be compromised in any way. This meant that, for example, large radiators on the largely glazed side walls and the radiant ceiling panels that are otherwise frequently used in halls were ruled out from the outset. “The comparatively high installation effort required due to the wooden beam construction was also a weighty argument against radiant ceiling panels,” says Dennis Ernst, Managing Director of the specialist HVAC company Heizung-Sanitär Niessen from Erkelenz that was carrying out the work.
In addition, localised heat loads in the area of the hangar ceiling had to be avoided at all costs: Despite the dimensions of the hangar, Blimp “Theo” and, in future, “Zeppelin NT” will be so close to the heat distribution system installed at a height of almost 26 metres that a direct impact on the outer skin of the airships had to be prevented, especially at higher temperatures.
The resulting “squaring of the circle” was resolved by the new type of Arbonia radiant ceiling profiles Cross supplied via the specialised wholesaler Gottschall & Sohn KG (Grevenbroich). These are very lightweight extruded aluminium strip profiles that can be easily joined together in any length using a connector system. Thanks to their Y-contour, they provide a larger radiant surface area despite their very slimline appearance with a width of only 17 cm and a height of 10 cm, which from an output point of view, performs about twice as well as a classic, but much more bulky-looking radiant ceiling panel. “Incidentally, being bulky would also have had a direct impact on the installation,” says Niessen Managing Director Dennis Ernst, recalling the initial coordination discussions and calculations in the run-up to the project: “Finding a way to fit the heavy panels between the rafters at a height of almost 26 metres would have been enormously time-consuming. When roughly calculating installation costs, we quickly reached a significant six-figure sum. This was not really economically justifiable. Especially as there was already a considerably more attractive solution available with the Cross® profiles ...”
Divided into two heating circuits, around two dozen of these profiles, which were installed in half the time, now run as a two-piece cascade along the entire length of the hangar dome. “The two-piece cascade, i.e. flow/return in separate cross profiles connected to each other at the end, was of course partly due to the heating load, which we cover here with our innovative heat distribution system at a flow temperature of 45 °C with an output of around 350 kW,” says Udo Fröhlig, Product Account Manager at Arbonia, explaining the technical background: “On the other hand, we also have to ensure a turbulent flow over the entire length of 55 metres for optimum heat transfer. This design meets these requirements perfectly.”
In total, the Niessen building services specialists installed around 1700 metres of Cross profiles, which are connected to the two heating circuits, which are also controlled separately, according to the Tichelmann principle. This ensures maximum energy efficiency and at the same time supports the most even heat distribution possible. Regardless of how strong the sunlight is on one side of the huge hangar, for example. This argument is all the more convincing as the hangar can be temperature-controlled in the same way via the cross-installations if required: “Up to 4 K reduction in room temperature is then possible, for example in conjunction with a corresponding heat pump,” says Christian Lutz (Arbonia Area Manager), pointing out a welcome additional benefit of the new heat distribution system.
Performance proven in practice
WDL Managing Director Frank Peylo is more than satisfied with this heat distribution system based on real-life experience after the first six months:
“The long aluminium profiles in the ceiling construction are not perceived by our guests as heating at all, but as an interior design element! At the same time, however, we have managed to heat the hangar to the required interior temperature of 22 °C for an event with 850 people – 1 K per hour – even in winter with an outside temperature of around 6 °C, using an acceptable amount of energy.”
At that point, heat was still generated using a mobile heating centre, as the final decision on the ultimate heating technology has not yet been made (as of July 2023). This is also linked to the WDL Group's aim of the realisation of the new airship hangar being as innovative and forward-looking a project as possible, says Frank Peylo, outlining the task that now needs to be completed:
“For most weeks of the year, we only need a basic load if the hall is only being used as a 'large garage' for the airships. On the other hand, very high loads have to be provided at short notice for events, but we want to generate them in a way that is no less resource-efficient.”
As a result, a hybrid system consisting of an air/water heat pump and a peak load boiler, possibly also based on renewable energies, could be used. But here, too, Frank Peylo's team remains true to the principle that applied to the new hangar building in general: to approach the project with as open a brief as possible – and correspondingly innovative partners – and thus create something that is unique in the world. Thanks to the innovative Arbonia Cross heat distribution system, the WDL Group has certainly already achieved this goal in terms of the overall architecture, the load-bearing structure, the versatile uses and, last but not least, the thermal comfort in the room.
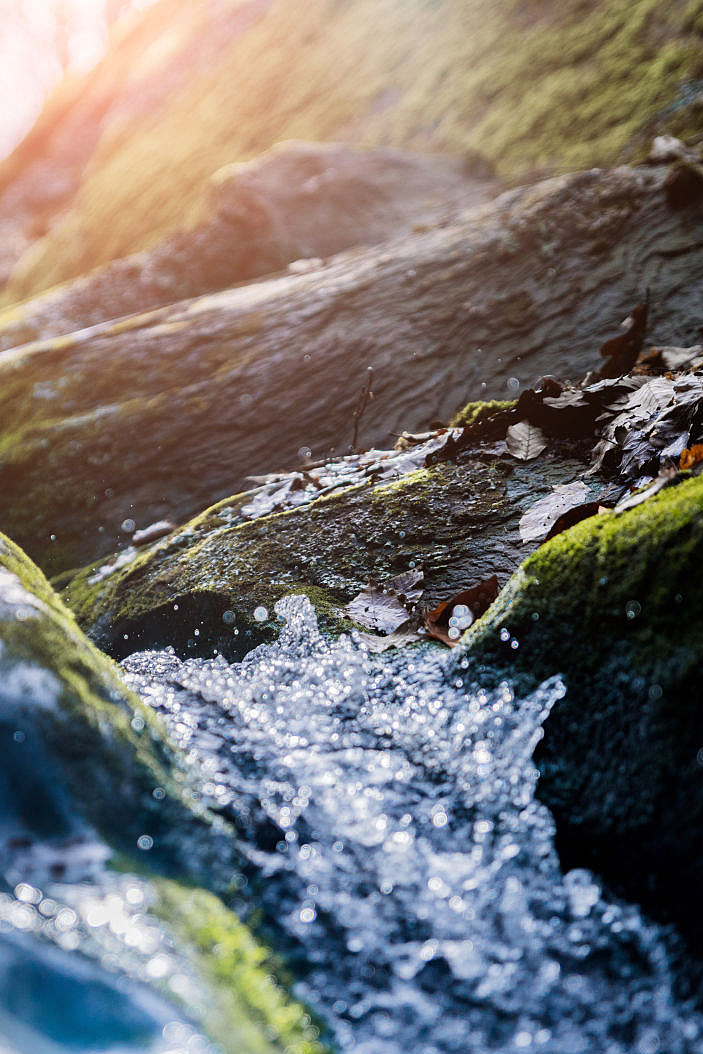
Images for property report
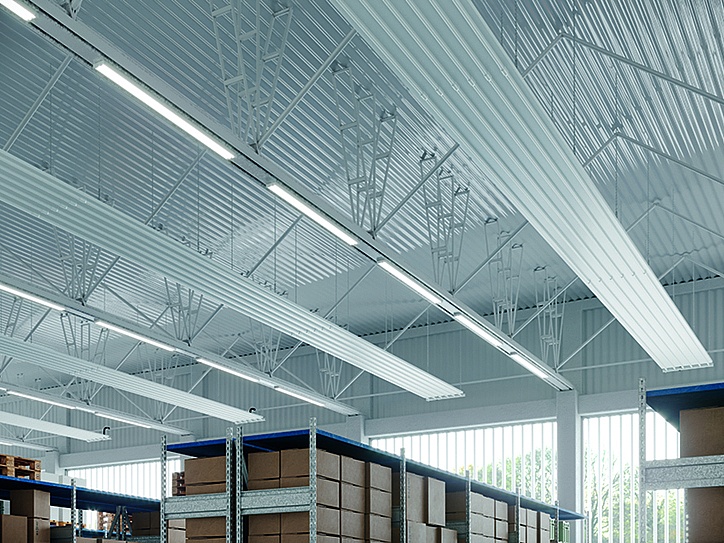
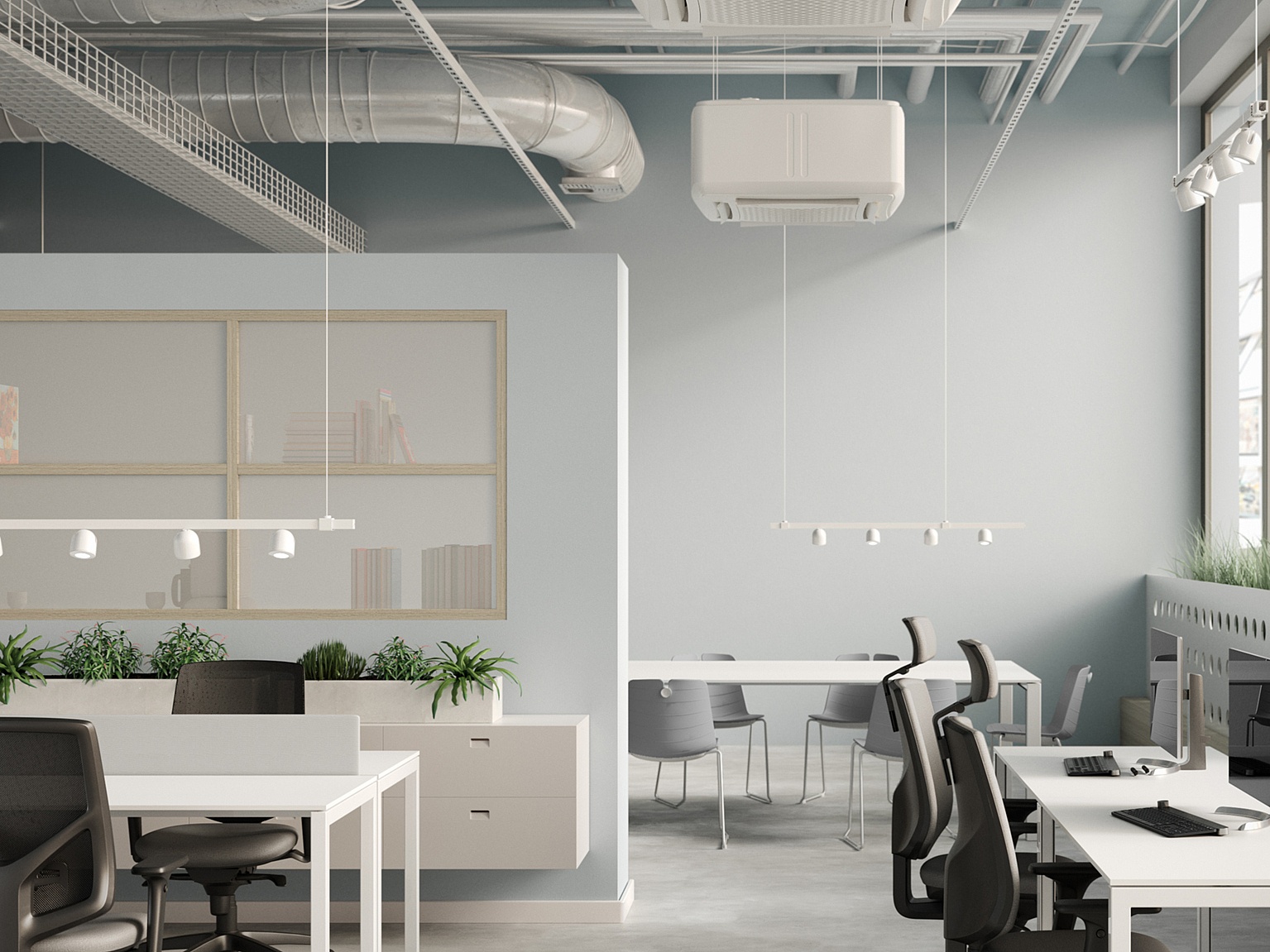
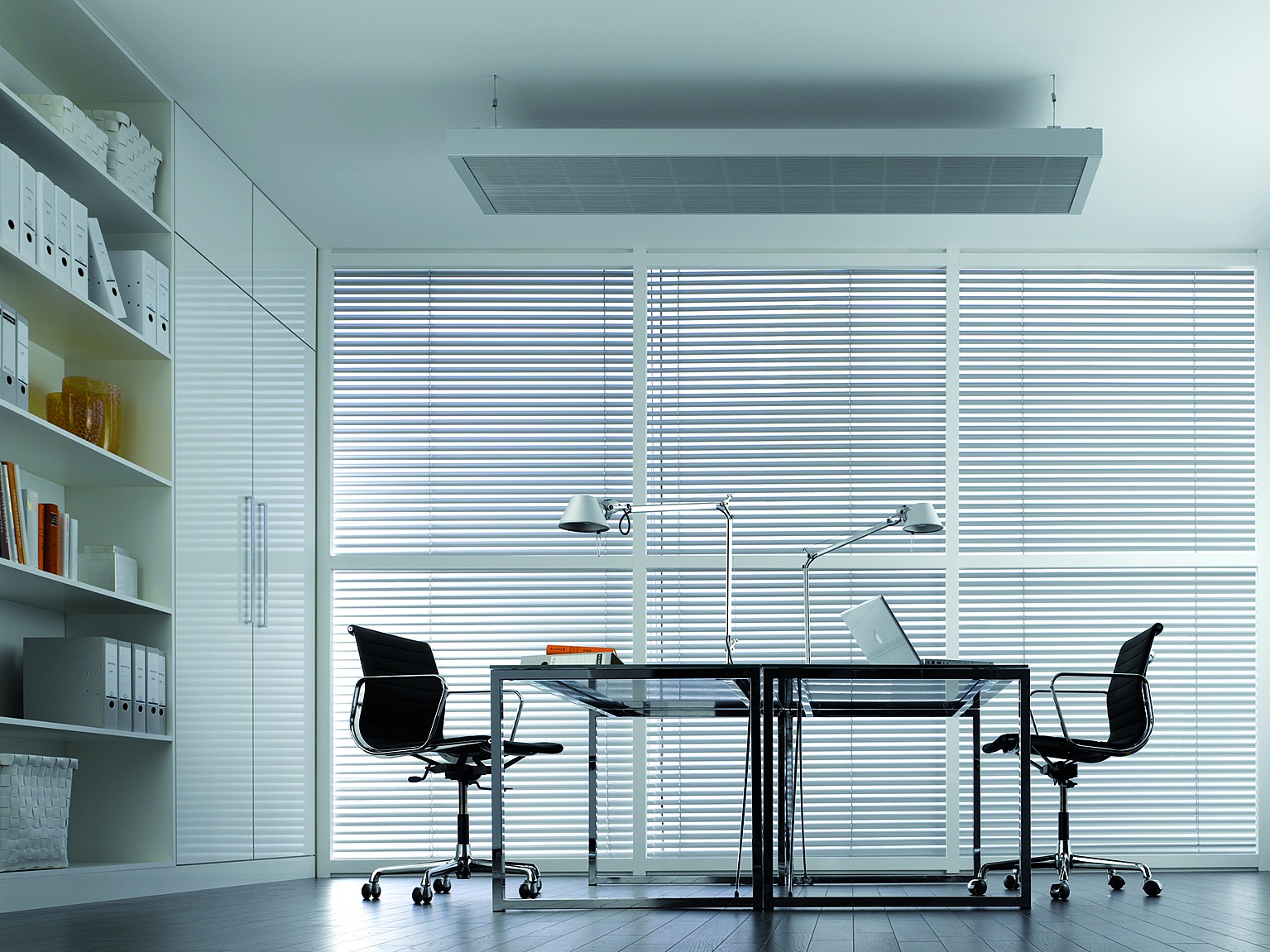
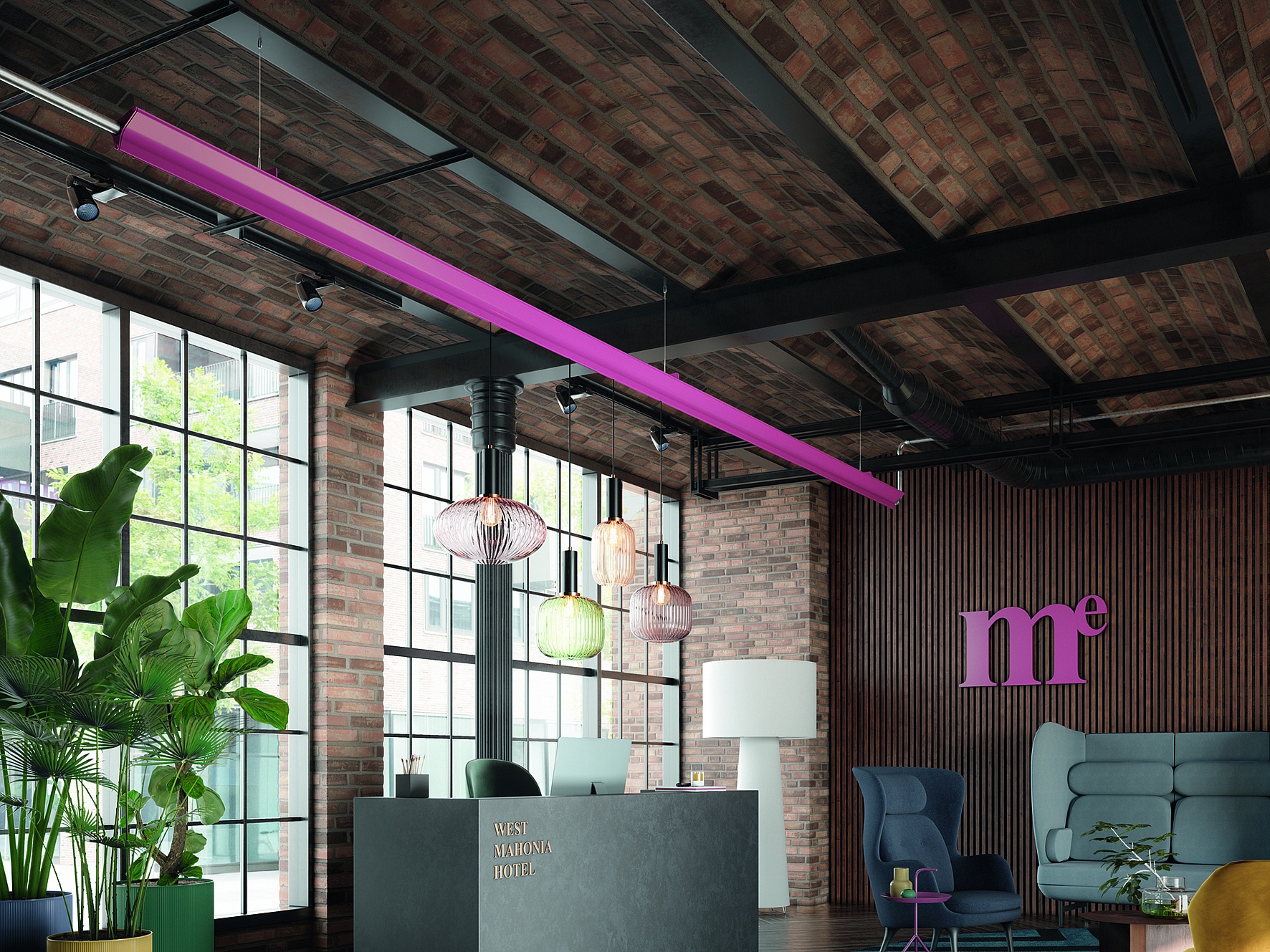